Das Problem: Mehr als fünfhunderttausend Tonnen Autoschrott fallen jedes Jahr in Deutschland an.
Die Lösung: Zwei junge Unternehmer machen aus Airbags und Gurten strapazierfähige Rucksäcke.
Zum Glück waren die beiden neu eingeschriebenen Studenten in Rotterdam naiv genug, mit ihren Fahrrädern zum Schrottplatz zu fahren. Adrian Goosses und Michael Widmann wollten für ihr erstes Semester in »Strategic Entrepreneurship« ein cooles Recycling-Projekt suchen; vielleicht alte Reifen in bequeme Sessel umwandeln oder so etwas. »In Rotterdam fahren ja alle mit dem Rad«, erinnert sich Goosses, 32, via Zoom aus seiner Heimatstadt Köln. Widmann und er kannten sich vor dem Studium nicht, aber landeten zufällig in der gleichen WG und verstanden sich auf Anhieb. »Die Reifen waren viel zu schwer und unhandlich, um sie aufs Fahrrad zu wuchten!«, sagt Widmann, 31, der per Zoom aus Bozen zugeschaltet ist. Also sahen sich die beiden um und fanden etwas Handlicheres im Autoschrott: Airbags und Gurte aus einem verunfallten Kleinwagen. Könnte man daraus einen nachhaltigen Rucksack basteln? Von der Größe her passte der Airbag schon mal. »Mit Faden und Nadel haben wir den ersten Prototypen genäht«, erzählt Goosses. »Dabei konnten wir gar nicht nähen.«
Zu ihrer Überraschung waren die Kommilitonen von dem Schrottsack so begeistert, »dass wir dachten, wir müssen das weitermachen«, sagt Goosses. »In jedem Semester haben wir an dem Konzept weitergearbeitet.« Mit Hilfe von YouTube-Videos brachten sie sich selbst das Nähen bei. Weil moderne elektrische Nähmaschinen an dem zähen Nylon der Airbags scheiterten, kauften sie sich im Secondhandladen für 10 Euro eine alte Singer von 1880. Die ersten Airbags färbten sie selbst in einem Kochtopf im Garten. »Am Ende des Masterstudiums hatten wir einen Businessplan und einen guten Prototyp.«
Die beiden haben 28.000 Gurtschlösser, 80.000 Airbags und 100.000 Sitzgurte weiterverarbeitet. Das entspricht etwa 60 Tonnen Autoschrott
Inzwischen betreiben die beiden Gründer eine florierende Firma für Backpacks aus Airbags: Airpaq. 2017 sammelten sie mit Crowdfunding ihr Startkapital von knapp 70.000 Euro. »Innerhalb von zwei Stunden hatten wir das Geld«, sagt Goosses, und die Verblüffung darüber ist ihm noch Jahre danach anzusehen. Seither haben die beiden 28.000 Gurtschlösser, 80.000 Airbags und 100.000 Sitzgurte zu neuen Produkten weiterverarbeitet. Das entspricht etwa 60 Tonnen Autoschrott. Für diese erfolgreiche Umsetzung bekamen sie unter anderem letztes Jahr den Deutschen Nachhaltigkeitspreis.
Die Singer-Nähmaschine ist längst Geschichte und nur noch Zierde im Kölner Büro. Inzwischen produzieren sie 500 Rucksäcke, Bauchtaschen und Sportbeutel pro Woche, mit einem Team von insgesamt 12 Leuten. Die Beutel werden professionell in Rumänien per Laser zugeschnitten, gefärbt und genäht. Die Rohmaterialien bekommen sie direkt aus dem Ausschuss eines Autozulieferers in der Nähe; niemand braucht also Angst haben, dass der Stoff des neuen Rucksacks in seinem letzten Leben schon in einen Unfall verwickelt war. Nur die Gurtschlösser kommen nach wie vor vom Schrottplatz, für knapp zwei Euro pro Stück.
Weil Airbags und Sitzgurte Leben retten, dürfen sie keinerlei Mängel aufweisen. »Selbst wenn irgendwo eine winzige Faser absteht, wird gleich die ganze Charge weggeworfen«, sagt Widmann. Genau das macht das Material für Rücksäcke ideal: »Das ist so strapazierfähig, das ist fast unkaputtbar«, erklärt Goosses und demonstriert mit einem scharfen Ruck, dass das Nylon selbst dann nicht weiter aufreisst, wenn schon ein Loch drin ist. Außerdem ist der Stoff wasserabweisend und sehr leicht. Ginge es um Baumwolle oder dünneres Polyester, könnte man immerhin noch Blusen oder Putzlappen daraus schneidern. Das Schweizer Unternehmen Freitag wandelt mit einem ähnlichen Upcycling-Gedanken und aus dem gleichen Grund, also weil das Ausgangsmaterial so zäh ist, LKW-Planen in Taschenunikate und Accessoires um.
Mit Preisen von 100 bis 160 Euro sind die Rucksäcke »derzeit nicht konkurrenzfähig,« sagen die Gründer selbst. Deshalb haben sie kleinere und billigere Produkte wie Bauchbeutel ins Sortiment aufgenommen. Aber natürlich kann man sich für 20 Euro einen Billig-Rucksack beim Discounter kaufen. Widmann und Goosses ist klar, dass sie die Preise senken müssen, aber bei Airpaq geht es nicht in erster Linie um Geld. »Es wäre natürlich billiger, wenn wir wie fast alle Textilanbieter in Asien nähen lassen würden«, weiß Goosses. Das kam für ihn nicht in Frage: »Schrott nach Vietnam verschiffen und dann zum Dumpingpreis nähen lassen? Nee, das ist ja alles andere als nachhaltig.«
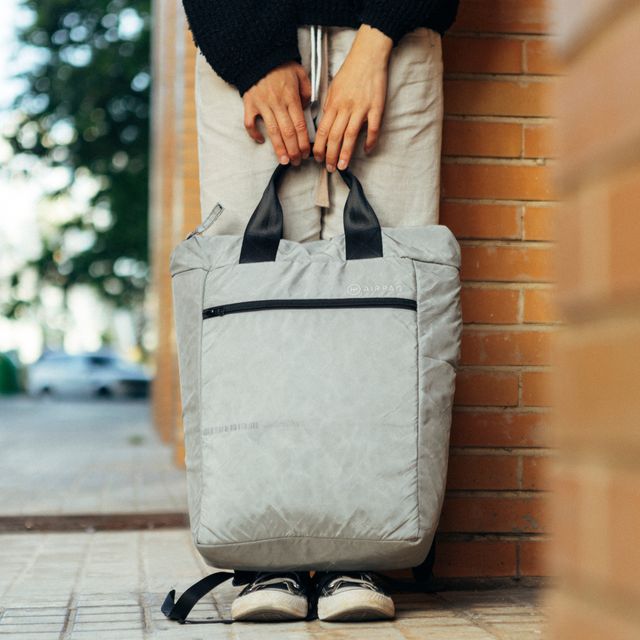
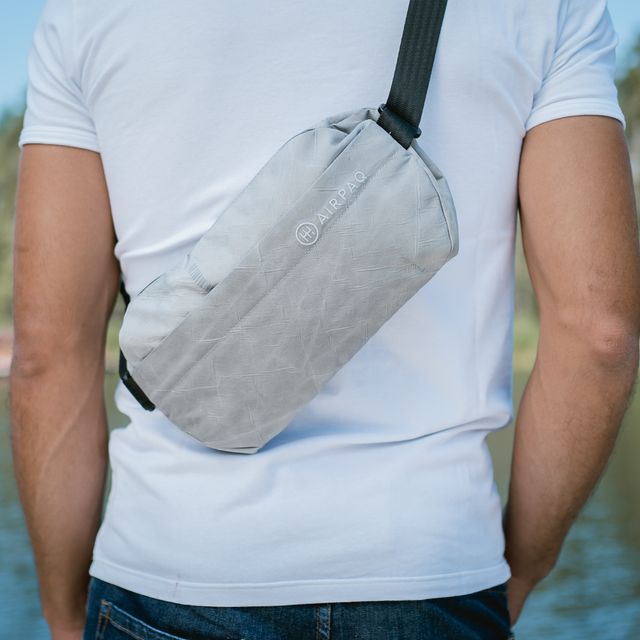
Neben Rucksäcken (links) und Slingbags (rechts) stellt Airpaq auch Bauchtaschen und Turnbeutel her.
Fotos: Airpaq
Die Familie des gebürtigen Südtirolers Michael Widmann betrieb bereits eine Näherei in Rumänien, allerdings für dünne, elastische Sporttextilien. Die Gründer durften dort die ersten Prototypen fertigen, mussten dann aber ihre eigene Produktion aufziehen. Sie zogen für sechs Monate nach Rumänien, »um die Menschen dahinter kennen zu lernen.« Schließlich wurde Goosses klar, dass sich hier der Kreis schließt. »Meine Mutter ist aus Rumänien, und unsere erste Näherei ist in ihrer Geburtstadt, ein verrückter Zufall.« Der zweite Produktionsstandort ist inzwischen in Timisoara. »Da wurde mein Opa geboren«, sagt Goosses.
Die Gründer achten auf kurze Transportwege. 20 Kilometer sind es vom Ausschusslager des Autoteilherstellers zu den Näherinnen. Sie betonen, dass die Näherinnen faire Löhne bekommen und Öko-zertifizierte Materialien zum Färben verwendet werden. Die Abwässer werden in einer eigenen Kläranlage gereinigt. »Herkömmliche Verfahren brauchen fünf bis sechs Liter Wasser pro Kilo Material«, erklärt Widmann. »Wir benötigen nur einen Bruchteil, weil die Farben von Hand einmassiert werden: 100 ml Wasser pro Kilo zum Waschen und Färben.«
Aber jedes Mal, wenn sich die beiden auf Schrottplätzen umschauen, haben sie mehr Ideen. »Wenn man sieht, wie viele Materialien da zur Verfügung stehen…«, sagt Widmann kopfschüttelnd und beendet den Satz nicht. »Wir wollen, dass Upcycling der neue Standard wird«, greift Goosses den Gedanken auf. »Man muss nur mit Kreativität rangehen, um Upcycling in den Mainstream zu bringen.«
Und vielleicht wird es dann doch noch was mit der Anfangsidee von den Autoreifen. »Man könnte aus den Reifen die Sohle für bequeme Schuhe machen«, überlegt Widmann laut. Dafür haben sie bereits den passenden Firmen-Slogan gewählt: »Schrott sei Dank, die Reise geht weiter.«